Advanced new automatic food cold storage
- 2018-05-02 14:05
- Automatic food cold storage logistics system pallet shelf
The Institute of automation of Beijing machinery industry has built a new type of automatic finished cold storage for a large food multinational company overseas. It has the characteristics of automatic stacking, automatic access and automatic sorting. It helps to build advanced logistics system and improve the production management level of the enterprise.
In recent years, new cold storage in Europe and America has begun to appear in China. Its main feature is single story elevated cold storage. One is the internal space of more than 10m, the use of shelves and high forklift, through the hall and to do the tally room, the width of more than 20m, reflecting the functional characteristics of the logistics cold storage. The other is an automatic stereo cold storage with automatic storage, automatic access and automatic sorting. Its internal space is up to more than 20 m, and the mechanization, automation and access efficiency are greatly improved, and the energy consumption is relatively low.
A world-famous large multinational food company has great influence in the industry. Its products sell well all over the country and are exported to overseas markets. The project introduced in this paper is a new type of fully automated three-dimensional cold storage built by the Beijing Institute of mechanical industry automation (abbreviated "North self") for the overseas branch of the company. It is characterized by automatic stacking, automatic access and automatic sorting. It has a certain representation in the food industry of Europe and the United States and the cold chain industry.
1. An overview of the project
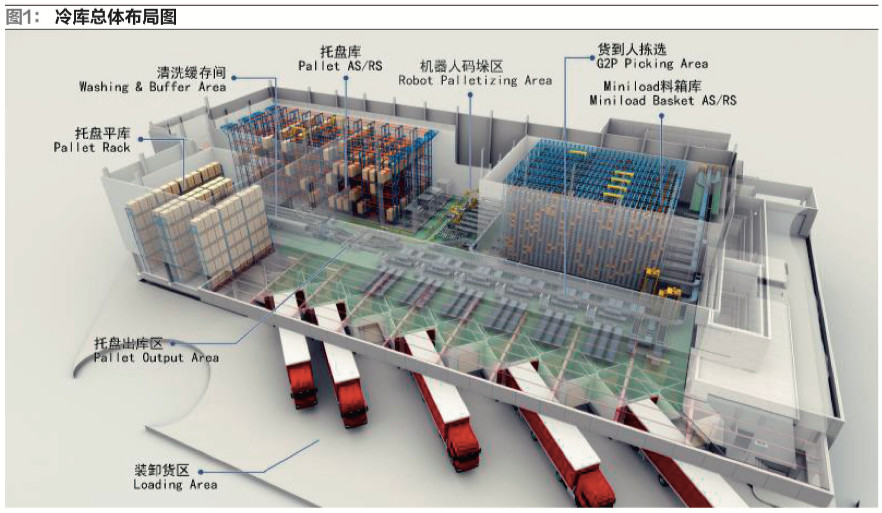
This automatic product library project includes pallet shelf system, tray stacker system, tray conveyer system, box type shelf system, Miniload stacking machine, box conveyor line system, palletizing system, protection facilities and related facilities. The whole warehouse is mainly composed of six functional areas: pallet shelf storage area, palletizing area, tray storage area, material box shelf storage area, goods to person picking area, and caching area, which can meet the storage of nearly 1000 pallets and more than 12000 turnover boxes. One hour can complete 100 pallets and 1960 turnaround volume. The box is out of the warehouse.
Two. Process design
After the finished product is packed in the workshop, it automatically spurts code on line and sends it to the front of the palletizing robot to carry out the encoder. Palletizing completed pallets pass through the cold storage transition to the stereoscopic storehouse before being sent from pallet stacker to storage in the storehouse. When the whole tray is out of storage, the tray stacking machine is taken out from the cargo position and sent to the outlet through the transport system. The forklift worker puts the pallet goods in the corresponding stock area according to the LED display display.
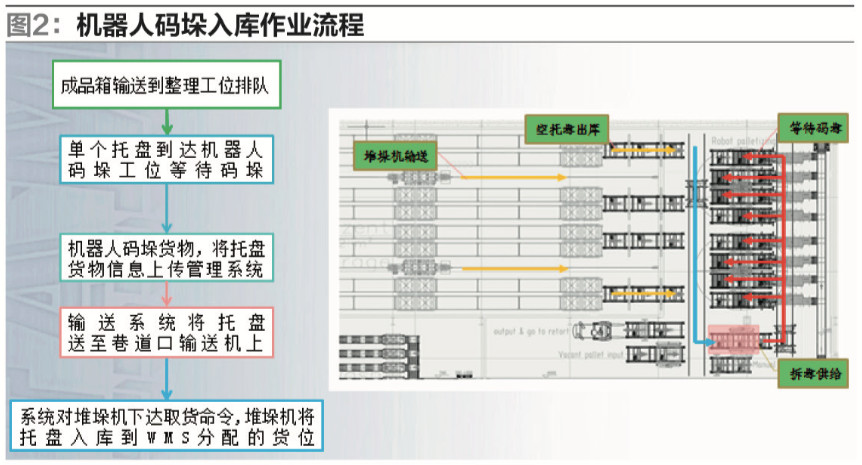
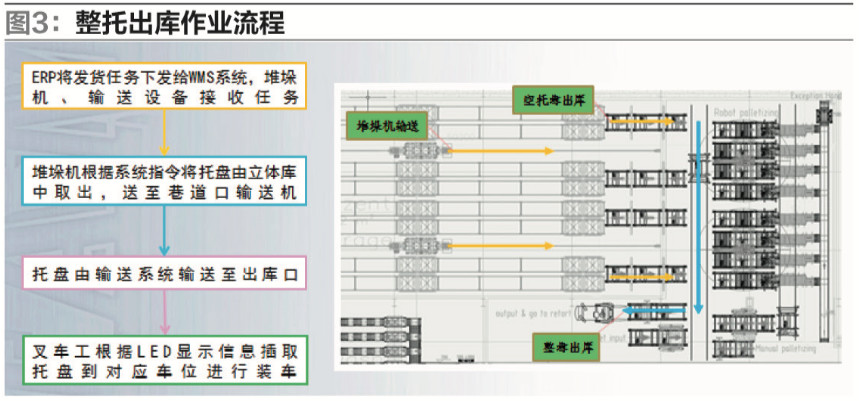
Miniload shelf area products are mainly seleced as single parts. The product is automatically placed in the turnover box in the workshop and sent to the library by the box conveyor line. The Miniload stacking machine also inserts two boxes into the storage at the same time. When the system sends out the picking task, the Miniload stacker inserts the corresponding turnover box out of the warehouse, and delivers the order picking task to the goods to person picking system. The order boxes are stacked into 12 piles. The workers use the help equipment to send stacked order boxes to the stocking area for temporary storage, and the picking boxes are sent back to the storehouse by the transmission lines.
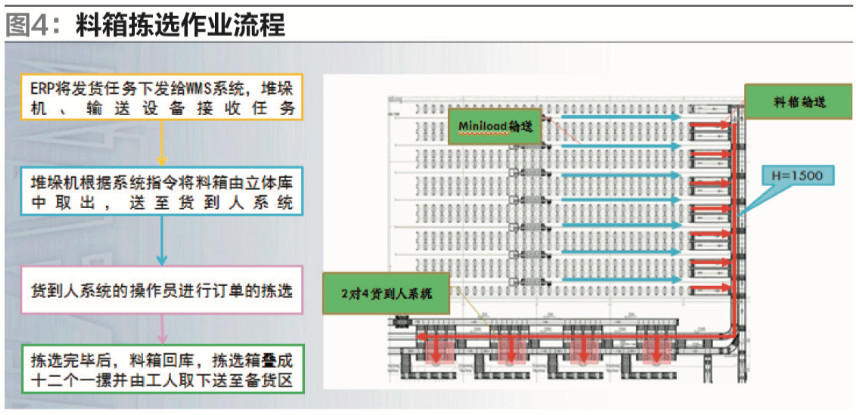
The empty turnover box produced after the picking up of the cargo arrival system is sent to the washing machine by the conveying system. The cleaning machine automatically clean the inside and outside of the turnaround box, then use the room temperature clean wind and wind to clean the liquid drops on the wall of the container, then dry it with 85 degrees of high temperature clean wind, and finally cool the turnover box to the normal temperature with the normal temperature clean wind. Part of the washing and drying box is sent to the workshop for reuse, part of which is sent to the storehouse for storage.
Three. Analysis of key technology
Miniload stacker can directly access plastic boxes and cartons, etc., and can realize intensive storage, quick picking and delivery. There are 7 laneways and 3000 freight spaces in the bin storage area of this project. The shelf height is about 12m. The Miniload stack machine selects the imported brand, uses the servo motor and the double station form, the horizontal running speed is 200m/min, the lifting speed is 60m/min, the fork speed is 40m/min, the single equipment can satisfy the 280 cases per hour entry and exit quantity.
The goods to person pick up station system includes 6 goods to the person picking workstation, each goods to the artificial bit using 2 to 4 forms, support 4 sowing sites at the same time sowing, according to the type of the sowing commodity box, the upper electronic label can indicate the container cargo box should be placed. Maximum flow rate, handling 2000 customer containers per hour.
The cargo arrival system includes a cargo arrival order processing system. The goods to person order processing system is the command and control center of the delivery system of the goods to the human order, supporting various types of order processing stations, and working together with WCS, conveyor control system and automatic access system to ensure the rapid, accurate and orderly completion of the related business related business, so as to improve the overall operation of the logistics center. Efficiency and management level.
Four. Analysis of the characteristics and benefits of the project
The integrated technology, equipment and software used in this project have good performance and price ratio. It is a mature technology used in several engineering examples. It has high advanced and practicability. In order to meet the needs of the customer's business, as a system integrator, in order to achieve the highest comprehensive efficiency of the logistics system, the most appropriate use of the same type of product is chosen to avoid unnecessary investment surf for the one-sided pursuit of the high speed of single machine equipment.
The implementation of this project helps customers build advanced logistics systems, establish the real-time connection between logistics information system and enterprise ERP system, improve the level of enterprise production management; space utilization rate reaches more than 3 times of the traditional warehouse; the goods change from "static storage" to "dynamic storage", and use automatic packing and palletizing. The system and advanced cargo arrival system have reduced more than ten workers and reduced the cost of labor.
Source: cold chain observation, the front line of cold chain actual combat