Stock base - cargo position system
- 2018-06-11 11:16
- Warehouse location system WMS inventory picking
The second chapter: the stock base -- the freight position system
If the warehouse is a whole big tree, then the leaf is equivalent to one item, and the supporting system is the cargo location system.
In fact, the freight position system is the most basic part of the WMS. The design of the cargo position system, to a great extent, determines the performance of the WMS system, especially the operation related to the stock transfer (including the shelves, picking, ordering, inventory, etc., which includes the efficiency and accuracy of most of the operations in the warehouse).
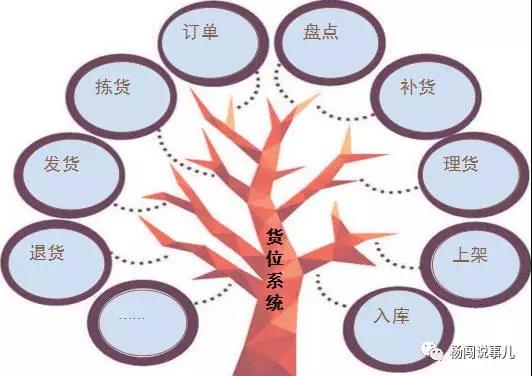
?
Cargo location system also develops from simple to complex development step by step with the development of B2C industry and the needs of business. Here are three kinds of cargo location system from simple to complex:
1. the simplest place of goods -- "one-to-one correspondence"
A. divided the warehouse into many blocks, named Location 1 and Location 2 respectively.
B. put a SKU in one area, and then record this information, forming a SKU and Location (cargo location) one to one correspondence form.
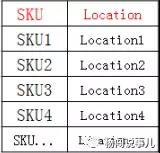
Every time C. places a product or a product in a library, look at the table first, see which SKU has a record, put it in the Location in the record, or go to the corresponding place, which products have not been recorded, and then add the Location information to the table.
Note: as long as this procedure is maintained, all SKU's location information will be recorded in the form.
2. upgrades -- "multi to one"
The "one-to-one" cargo location system has solved some urgent problems, but the most obvious problem has been found in its application: the number of manageable SKU is limited.
Give an example:
10 thousand square meters of warehouse 4000 square meters for collection and operation, about 6000 square meters can be used for storage. In the storage area, the channel accounts for at least 60%, and the actual storage area is only 2400 square meters. Suppose there are 4 storeys on the shelf, 40cm per storey, and the actual storage area is 9600 square meters. The cross section of each Location is 60cm*60cm, that is, 0.36 square meters, and the total Location for use is 26 thousand and 700 (in the above calculation, the maximum storage capacity of each bit is only 0.6*0.6*0.4=0.144m3).
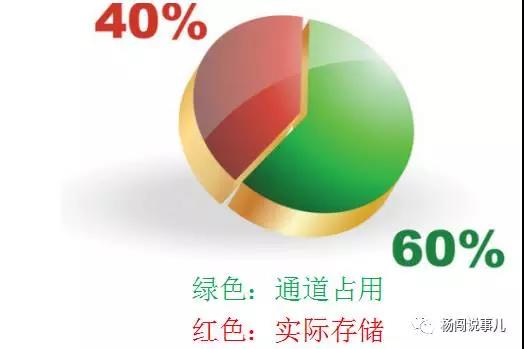
If you consider that there is a good seller, a large stock or a large volume of goods in SKU, the number of managed SKU will be even less.
To solve this problem, the one-to-one correspondence in tables is changed to many to one relations.
That is to store multiple SKU in the same Location, as follows:
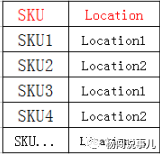
In this way, the number of manageable SKU increases is achieved. Using this method, the amount of manageable SKU can be increased by more than 2 times more than that of the basic version, according to the different types of SKU managed by the storeroom.
3. the prototype of the current position system -- "many to many"
The use of "multi to one" system can greatly improve the number of SKU in the warehouse management, but the same problem: after a large amount of SKU stock, it may be subject to the quantity of inventory instruments and the number of errors, the situation can not be completely put down in the cargo position.
Many pairs of relationships have emerged in response to this problem.
That is, one SKU can be placed in multiple Location, and one Location can store more than one SKU.
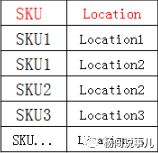
01 this system has obvious advantages
First, the system architecture is relatively simple, only to maintain a single form, with only two data items in the table, and all the operations are handled only for the information line of the table.
Secondly, the operation on the shelf is relatively simple. When the operation is on the shelves, the pick up clerk first inquires whether there is already a cargo location. If there is already a cargo location, it will be placed on the existing cargo space. If not, then the new cargo location will be available. If you can't put down the product on the original cargo location, you can find another place that can be lowered directly, and add the corresponding relationship to the form.
Third, "many to many" system costs low, all operations (including shelves, picking, moving goods) can be completed on the computer.
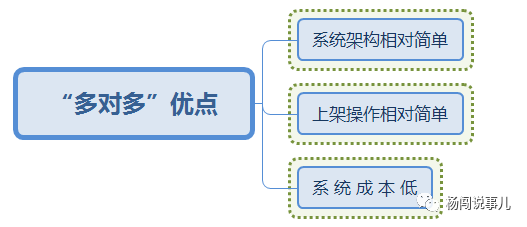
02 but this system has some shortcomings
First, the redundancy of information is inevitable. For example: Location N on top of the SKU N, and later in the process of successive shipments, SKU N was picked out one by one, and finally Location N on the top and no SKU N, but the system still shows that SKU N is on the goods.
Second, the efficiency of picking is not high. When a SKU exists in multiple Location, the picking clerk needs to decide which Location to pick up. If there is a problem of redundant information in the previous location, it is possible for the picking personnel to run for one trip, which has a great impact on the picking efficiency.
Third, it is difficult to check. A SKU in a number of cargo locations, inventory time to run around, very troublesome, and easy to make mistakes.
Fourth, the picking path is inefficient. In the case of picking up dozens of picking orders at the same time, in the case of multiple Location in a SKU, the picking personnel may need to travel through all the Location to complete the task of picking, and the efficiency is affected.
Fifth, the error rate of picking is high. Because the picking process of the cargo location system is entirely manual operation, and there is no system selection, so the error rate is high. For example, picking and picking wrong.
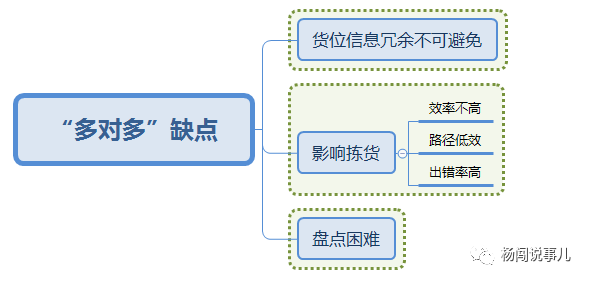
Countermeasures
A. clean up redundant information:
Regularly check all SKU with more than two cargo locations and delet redundant useless information.
B. regular geographic goods:
For example, we should move the hot products to the larger area of the cargo location and move the slow products to the smaller areas. Or the same product dispersed in multiple locations.
C. daily operation management:
1. when the location of a product is already there, and there is stock on the stock, try not to add new freight.
2. when the original position is unable to store all stocks, a larger cargo location can be found, wher all the stocks are placed and the original cargo location is deleted.
3. similar products are not placed in the same place;
The above points can reduce the shortcomings of the inventory system, but can not be eradicated. How to eradicate it? Third chapters to be continued...
Source: JitLogistics and Yang Chuang